A Comprehensive Overview to the Process and Benefits of Plastic Extrusion
In the substantial realm of manufacturing, plastic extrusion arises as a crucial and highly effective procedure. Translating raw plastic right into continuous profiles, it caters to a variety of sectors with its remarkable flexibility.
Comprehending the Essentials of Plastic Extrusion
While it may show up complicated at very first glance, the process of plastic extrusion is essentially basic. The procedure starts with the feeding of plastic product, in the form of powders, granules, or pellets, into a warmed barrel. The designed plastic is then cooled down, strengthened, and cut right into preferred lengths, finishing the process.
The Technical Process of Plastic Extrusion Explained

Kinds Of Plastic Suitable for Extrusion
The selection of the best kind of plastic is a critical aspect of the extrusion process. Various plastics use one-of-a-kind homes, making them extra matched to particular applications. Polyethylene, for instance, is commonly used due to its low cost and easy formability. It provides outstanding resistance to chemicals and wetness, making it optimal for items like tubing and containers. Likewise, polypropylene is another popular choice due to its high melting factor and resistance to exhaustion. For more durable applications, polystyrene and PVC (polyvinyl chloride) are usually selected for their strength and resilience. Although these are common options, the choice ultimately relies on the certain demands of the product being generated. Understanding these plastic kinds can substantially enhance the extrusion procedure.
Contrasting Plastic Extrusion to Other Plastic Forming Techniques
Understanding the sorts of plastic suitable for extrusion leads the means for a wider conversation on how plastic extrusion piles up against other plastic creating methods. These consist of shot molding, blow molding, and thermoforming. Each approach has its unique uses and benefits. Injection molding, for example, is excellent for developing intricate parts, while impact molding is perfect for hollow items like containers. Thermoforming excels at forming big or superficial parts. Nevertheless, plastic extrusion is unparalleled when it concerns producing continual profiles, such as gaskets, pipelines, and seals. It likewise enables a regular cross-section along the length of the product. Hence, the selection of approach largely depends on the end-product demands and specs.
Secret Advantages of Plastic Extrusion in Manufacturing
In the world of manufacturing, plastic extrusion provides numerous significant benefits. One notable benefit is the cost-effectiveness of the procedure, that makes it an economically appealing manufacturing approach. Furthermore, this method offers superior item adaptability and improved production rate, consequently boosting overall manufacturing performance.
Economical Production Method
Plastic extrusion leaps to the forefront as an economical manufacturing technique in production. In addition, plastic extrusion calls for much less power than typical manufacturing methods, contributing to lower operational costs. YOURURL.com Overall, the financial benefits make plastic extrusion a highly attractive option in the production sector.
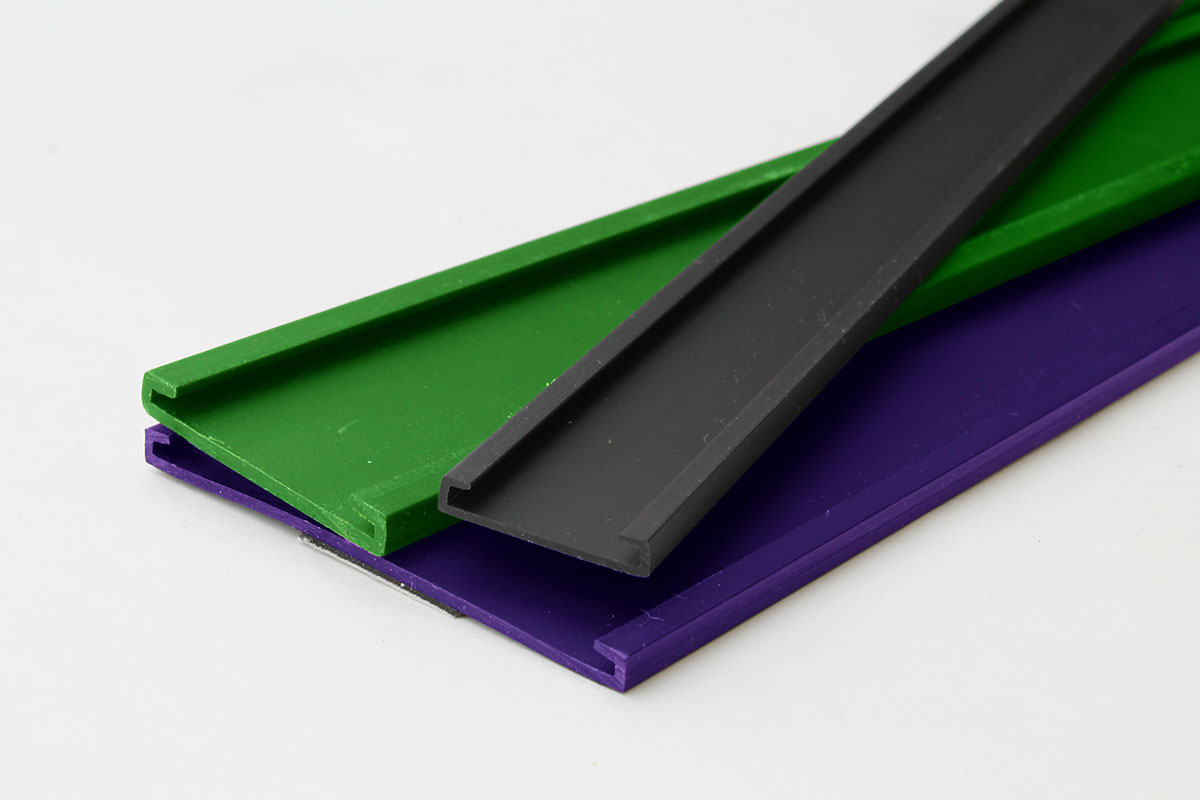
Superior Product Flexibility
Beyond the resource cost-effectiveness of plastic extrusion, another substantial benefit in producing depend on its superior item versatility. This process enables the development of a large range of products with differing shapes, designs, and dimensions, from straightforward plastic sheets to complex profiles. The adaptability is associated to the extrusion die, which can be tailored to produce the desired item design. This makes plastic extrusion a perfect solution for sectors that need tailored plastic elements, such as automotive, construction, and product packaging. The ability to create diverse items is not just helpful in meeting certain market demands however also in allowing manufacturers to check out brand-new product with marginal capital expense. In significance, plastic extrusion's product adaptability fosters advancement while enhancing operational effectiveness.
Enhanced Production Speed
A substantial advantage of plastic extrusion depends on its enhanced production speed. This manufacturing process permits high-volume manufacturing in a reasonably brief time period. It is qualified of generating long, continuous plastic profiles, which considerably decreases the production time. This high-speed manufacturing is particularly advantageous in markets where big quantities of plastic parts are needed within tight due dates. Few other manufacturing processes can match the speed of plastic extrusion. Additionally, the ability to keep regular high-speed manufacturing without giving up item high quality establishes plastic extrusion besides other methods. The enhanced production rate, consequently, not just allows makers to satisfy high-demand orders but also adds to raised performance and cost-effectiveness. This helpful feature of plastic extrusion has actually made it a favored selection in numerous sectors.
Real-world Applications and Impacts of Plastic Extrusion
In the world of manufacturing, the technique of plastic extrusion holds extensive importance. This procedure is commonly made use of in the manufacturing of a variety of items, such as plastic tubing, home window structures, and climate stripping. Because of this, it substantially influences fields like building, product packaging, and automobile sectors. Additionally, its impact includes day-to-day products, from plastic bags to tooth brushes and disposable flatware. The economic benefit of plastic extrusion, mainly its high-volume and affordable outcome, has actually transformed production. However, the environmental effect of plastic waste continues to be an issue. The industry is persistently striving for developments in recyclable and eco-friendly products, indicating a future where the benefits of plastic extrusion can be retained without compromising environmental sustainability.
Final thought
Finally, plastic extrusion is a efficient and extremely efficient method of changing basic materials into diverse items. It supplies many advantages over other plastic creating techniques, including cost-effectiveness, high output, marginal waste, and style versatility. Its impact is exceptionally really felt in various sectors such as building and construction, vehicle, and consumer goods, making it a crucial procedure in today's manufacturing landscape.
Diving deeper into the technological Look At This process of plastic extrusion, it starts with the choice of the appropriate plastic product. When cooled down, the plastic is reduced into the called for lengths or injury onto reels if the product is a plastic movie or sheet - plastic extrusion. Comparing Plastic Extrusion to Various Other Plastic Forming Techniques
Understanding the kinds of plastic appropriate for extrusion leads the method for a broader conversation on how plastic extrusion piles up against various other plastic developing methods. Couple of other production processes can match the rate of plastic extrusion.
Comments on “Plastic extrusion for intricate profiles and custom designs”